Understanding Belt Profiles: PowerGrip GT2, GT3, HTD, MXL, XL, L, 40 DP, T and AT
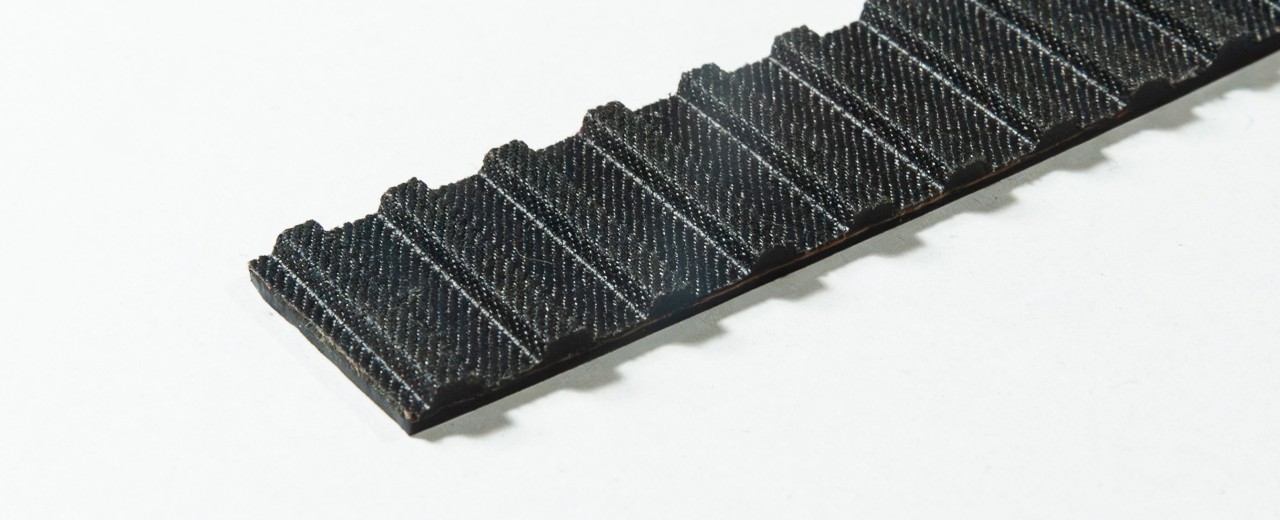
Belt profiles play a crucial role in synchronous drive systems. They influence efficiency, load capacity, noise, and longevity of the drive, with belt design being a key factor in selecting and specifying the right belt for various applications. This guide covers the most common belt profiles used in industrial applications: PowerGrip GT2, GT3, HTD, MXL, XL, L, 40 DP, T and AT. We’ll discuss their design, unique characteristics, and best use cases.
1. PowerGrip GT2 Profile
Overview and Key Features — The PowerGrip GT2 profile is a modern improvement over traditional HTD profiles. It features a deep tooth design that increases surface contact, improving load capacity and minimizing wear. This profile supports better synchronization, making it ideal for precision applications where accuracy is paramount.
- Tooth Design: Deep, curvilinear tooth profile with full flank contact.
- Load Capacity: Up to 200% more load capacity compared to previous PowerGrip or HTD profiles.
- Noise Reduction: Smooth meshing action reduces vibration and noise.
- Application Examples: Robotics, medical equipment, CNC machines, machine tools, conveyors, and servo drive systems.
Advantages
- Greater load capacity than HTD belts.
- Reduced vibration and noise.
- Longer belt life due to less tooth deformation and wear.
Best Used For: High-speed, high-load, and precision indexing applications.
TwinPower GT2
Gates TwinPower GT2 belts have teeth on both sides, offering precise synchronization from dual driving surfaces. This design allows unique drive setups such as multipoint drives, rotational reversals with one belt, or serpentine configurations. TwinPower GT2 belts are constructed similarly to standard synchronous belts, with helically-wound fiberglass cords embedded in a neoprene body, and both sides covered in durable nylon fabric. They deliver superior load capacity and precision, making them ideal for applications where space efficiency and accuracy are critical.
2. PowerGrip GT3 Profile
Gates' PowerGrip™ GT™3 belts are advanced rubber synchronous belts designed to enhance performance and reduce both initial and operating costs. They are suitable for new drive designs and can also serve as performance upgrades for existing drives.
Key Features:
- Enhanced Power Transmission: These belts can transmit up to 30% more power than previous generations, such as the PowerGrip™ GT2.
- Durable Construction: Built with a fiberglass tensile cord, elastomeric teeth and backing, and a nylon facing, they offer high strength, excellent flex life, and resistance to elongation.
- Versatile Applications: The 2MGT, 3MGT, and 5MGT pitches are ideal for compact drives found in hand tools, business machines, domestic appliances, and high-precision servomotor drives.
Specifications:
- Pitch Sizes: Available in 2mm, 3mm, 5mm.
- Temperature Range: Operational between -30°C to +100°C (-22°F to +212°F).
- Compatibility: The 2MGT, 3MGT, and 5MGT pitches fit GT™ profile pulleys.
For detailed design and tensioning guidelines, it's recommended to consult Gates' Synchronous Belt Drive Design Manual or use their DesignFlex® Pro™ Drive design software.
By choosing PowerGrip™ GT™3 belts, you invest in a solution that offers increased power ratings, compact drive designs, high positioning accuracy, improved tooth jump resistance, reduced noise levels, and a cost-effective, long-lasting, virtually maintenance-free operation.
Read more about PowerGrip GT®
3. HTD (High Torque Drive) Profile
Overview and Key Features — HTD belts are used in high torque applications. Unlike PowerGrip GT2, HTD belts have a larger tooth-to-groove clearance, resulting in higher backlash. Despite this, they excel in heavy-duty applications.
- Tooth Design: Semi-circular teeth with substantial clearance in the groove.
- Load Capacity: Built for high torque drive applications.
- Backlash: Higher than PowerGrip GT2, especially when used with small sprockets.
- Application Examples: Heavy machinery, conveyor belts, and material handling systems.
Advantages
- Capable of handling high torque.
- Reliable performance under shock loads.
Best Used For: Applications where torque capacity is more critical than precision, such as in industrial material handling systems.
TwinPower HTD
TwinPower HTD belts have a similar double-sided tooth construction, providing synchronization from both belt sides. Featuring helically-wound fiberglass tension members and a neoprene body with nylon-faced teeth, they offer balanced load distribution and durability. They are recommended for drives that need bidirectional power transmission, multi-point synchronization, or serpentine routing. HTD TwinPower belts are particularly useful where high torque capacity and reliable performance are essential.
4. .080" MXL Profile
Overview and Key Features — MXL belts are micro-pitch timing belts with a pitch of 0.080 inches. They’re widely used in small devices that require high precision and compact design.
- Tooth Pitch: 0.080 inches.
- Application Examples: Printers, medical devices, small robotics, and consumer electronics.
Advantages
- Ideal for compact spaces.
- Suitable for precise positioning and light loads.
Best Used For: Low-load, high-precision applications where space constraints exist.
5. 1/5" XL Profile
Overview and Key Features — The XL profile is a classic timing belt profile with a 1/5-inch pitch. It offers good torque transmission and positioning accuracy.
- Tooth Pitch: 1/5 inch (0.200 inches).
- Application Examples: Power tools, appliances, robotics, and small drive systems.
Advantages
- Excellent for torque transmission.
- Widely available as a standard timing belt option.
Best Used For: Light to medium-load applications where versatility and cost-efficiency are important.
TwinPower 1/5" XL
The TwinPower 1/5" (0.200") XL belts feature a classic double-sided trapezoidal tooth design, suited for compact drives requiring synchronized power from both sides of the belt. These belts offer versatility and cost-efficiency, frequently used in smaller-scale precision drives like power tools, robotics, and appliances.
6. 3/8" L Profile
Overview and Key Features — The L profile features a 3/8-inch pitch, making it suitable for larger, more powerful synchronous drive systems.
- Tooth Pitch: 3/8 inch.
- Application Examples: Industrial automation, conveyor systems, packaging equipment, and machine tools.
Advantages
- Greater load capacity than MXL or XL.
- Versatile in many power transmission applications.
Best Used For: Medium to heavy-duty industrial applications.
TwinPower 3/8" L
The TwinPower 3/8" L belts have a robust dual-sided synchronous tooth configuration, making them well-suited for medium to heavy-duty industrial applications. The double-sided teeth allow these belts to be effectively utilized in multi-point and serpentine drive applications, providing reliability and versatility for equipment like packaging machines and conveyors.
7. .0816" 40 DP Profile
Overview and Key Features — The 40 DP profile is unique due to its use of diametral pitch (DP) instead of inch or metric pitch. This profile is often found in legacy systems and specialized designs.
- Tooth Pitch: 0.0816 inches.
- Application Examples: Legacy systems, special machinery, and precise positioning systems.
Advantages: Ideal for specific, high-precision drives.
Can be retrofitted into existing systems using the 40 DP pitch.
Best Used For: Equipment that requires exact compatibility with 40 DP standards
8. T and AT Profiles
T and AT profiles are types of trapezoidal timing belt tooth designs commonly used in power transmission and conveying applications.
T Profile:
The T profile features a standard trapezoidal tooth shape and is defined by metric pitches such as T2.5, T5 and T10. These belts are versatile and suitable for various drive and conveying tasks.
AT Profile:
The AT profile is an advancement of the T profile, offering a larger tooth volume and stronger cords. This design enhancement leads to higher tooth load capacity and improved performance in high-torque applications. AT profiles are available in metric pitches like AT3, AT5 and AT10.
Key Differences:
- Tooth Design: AT profiles have a more robust tooth shape compared to T profiles, resulting in better load distribution and reduced backlash.
- Load Capacity: Due to their design, AT belts can handle higher loads and are more suitable for applications requiring precise positioning and high torque transmission.
Applications:
- T Profile: Ideal for general-purpose drives and conveying systems where standard load capacities are sufficient.
- AT Profile: Preferred in applications demanding higher load capacities, precise positioning, and reduced backlash, such as linear actuators and packaging.
When selecting between T and AT profiles, consider the specific requirements of your application, including load, speed, and precision needs. Proper selection ensures optimal performance and longevity of the belt system.
Conclusion
Each belt pitch has its strengths and best-use cases. Understanding their differences ensures you select the right profile for your specific application. Whether you’re working with robotics, heavy machinery, or compact devices, choosing the right belt profile can mean the difference between operational efficiency and costly downtime. If you’re unsure which profile fits your application, consult our specialist or review York Industries’ resources for technical assistance.
We have thousands of belts in stock, ready to ship. Need a specific width? No problem — we can cut belts to match your exact specs. Let us know what you need, contact us!